Aluminum is one of the most abundant metals in the Earth’s crust and comprises over 8% of its mass, making it a readily available resource for manufacturing countless products. This widespread availability, combined with its desirable properties, has fueled the growth of the aluminum casting industry. As of 2024, the global market for aluminum casting has reached $100.94 billion. It is also projected to expand at an annual rate of approximately 4.9% from 2025 to 2030, reflecting its increasing importance across many industries.
This article will discuss the various aspects of aluminum casting, covering the basics of this process, the different techniques involved, the suitable aluminum alloys, their applications, and several FAQs.
What is Aluminum Casting?
Aluminum casting is a manufacturing process used to create metal parts by pouring molten aluminum into a mold cavity. The liquid aluminum fills the mold, solidifies as it cools, and takes the shape of the cavity, resulting in a solid aluminum component. This can be achieved through several methods, which we will explore later in this article.
The origins of aluminum casting can be traced back to the mid-19th century, with Henry Bessemer’s 1854 work laying the groundwork for pressure casting. However, widespread adoption was hindered by the expense and complexity of producing aluminum at that time.
The crucial turning point came with the 1886 invention of the Hall-Héroult process, which simplified aluminum extraction and drastically lowered production costs. This innovation made aluminum commercially viable for casting and other applications, effectively launching the modern aluminum casting industry.
What are the Properties of Aluminum Castings?
Being nearly three times lighter than iron, aluminum castings are lightweight with a low density of 2,700 kg/m3. This gives them a significant advantage, especially in industries like automotive and aerospace where weight reduction is crucial. Despite that, aluminum still boasts a remarkable strength-to-weight ratio as its tensile strength ranges from 70 to 700 MPa, providing structural integrity without adding excessive weight.
Furthermore, aluminum has excellent corrosion resistance, protecting parts from environmental degradation and extending their lifespan. Its high electrical and thermal conductivity also makes it suitable for creating electrical components or applications involving heat transfer.
Besides, aluminum casting offers high machinability for intricate designs and precise tolerances, making it possible to create complex parts with high accuracy. It can even achieve a fine surface finish which enhances the final product’s aesthetic appeal and functionality. Due to these combined properties, aluminum castings are a versatile and valuable option for modern manufacturing.
How to Cast Aluminum: Common Types of Aluminum Casting Processes
Aluminum mold casting processes are mainly differentiated based on their mold material and mold filling methods. In this section, we will introduce common aluminum casting processes, mainly:
- Permanent Mold Casting
- Die Casting
- Sand Casting
- Investment Casting
- Centrifugal Casting
- Open Mold Casing
We will also briefly introduce some of their alternative casting techniques, where applicable.
Permanent Mold Casting
Permanent mold casting utilizes reusable molds typically made of steel or cast iron. When the molten aluminum is poured, it will rely solely on gravity to fill the mold cavity. This is why it is also called gravity casting.
This process results in castings with good surface finishes and improved mechanical properties due to the low turbulence and even cooling rates. Additionally, it has lower labor costs, especially for production with medium to low volumes, as the process is very straightforward. However, it is generally less suitable for highly complex designs than die casting or investment casting. The slower production rate also makes it less ideal for high-volume manufacturing needs.
Die Casting
Die casting involves injecting molten aluminum into a precisely machined steel mold, called a die, under significant pressure. There are two primary variations: high-pressure and low-pressure die casting, which differ mainly in the injection pressure used. High-pressure die casting uses extremely high speeds and pressures, enabling the production of thin-walled, intricate parts with excellent surface details. Low-pressure die casting employs lower pressures to fill the die which offers better control over the filling process, minimizing turbulence and porosity to result in stronger castings.
Thanks to the pressure maintained during solidification, die casting can produce complex shapes with tight tolerances, great surface finish, and consistent quality, reducing the need for post-processing. The rapid cycle times make it highly efficient for large production runs. On the other hand, die casting is less economical for small production volumes because the initial tooling costs for creating the dies are quite high.
Sand Casting
Sand casting employs sand as the mold material. The sand is mixed with a binding agent and packed around a pattern of the desired part to create a mold cavity, where the molten aluminum will be poured in. Unlike permanent mold casting and die casting, the sand mold is non-reusable so it will be broken away to retrieve the casting after the aluminum solidifies and cools. The sand will then be recycled to create new molds later on.
One of the key advantages of sand casting is its low tooling cost, as the molds are relatively fast and inexpensive to produce. This makes it particularly suitable for prototypes, small production runs, and large-sized castings. Nevertheless, the resulting castings typically have a rougher surface finish and lower dimensional accuracy than other methods, so they may require secondary machining or finishing operations, incurring additional costs.
Sand Casting Alternative: Shell Mold Casting
Some manufacturers may opt for a variation of sand casting called shell mold casting where a thin, hardened shell is created by coating a heated pattern with a resin-bonded sand mixture, forming a more secure mold cavity. This method offers improved dimensional accuracy and surface finish compared to traditional sand casting while still maintaining relatively low tooling costs and faster mold creation.
Investment Casting
Investment casting is also known as lost-wax casting or ceramic mold casting. The process begins with creating a precise wax pattern of the desired part. This pattern will be assembled into a group and coated with a ceramic slurry, which hardens to form a shell. The wax is then melted out, leaving a hollow ceramic mold for molten aluminum to be poured in. After solidification, the ceramic shell is broken away to reveal the final casting.
Investment casting offers excellent dimensional accuracy, intricate detail reproduction, and a smooth surface finish, making it ideal for complex geometries, especially in small to medium-sized parts. The downside of this process is it is more complex and time-consuming than other casting methods, resulting in production costs and longer lead times.
Investment Casting Alternative: Lost Foam Casting
Alternatives to investment casting include lost foam casting, where a foam pattern (typically polystyrene) is used instead of wax. The molten metal vaporizes the foam upon pouring, filling the resulting cavity. While this method is simpler, it may not achieve the same level of detail as traditional investment casting.
Investment Casting Alternative: Plaster Mold Casting
Another alternative is plaster mold casting, which uses gypsum plaster instead of ceramic for the mold itself. Even though this method produces a smooth surface finish, it is generally limited to lower-temperature metals like aluminum and zinc because the mold material cannot withstand high temperatures.
Centrifugal Casting
Centrifugal casting uses rotational force to create hollow, cylindrical parts. A mold is rotated at high speeds while molten aluminum is poured into it. The centrifugal force distributes the metal evenly against the mold’s inner wall. Once the aluminum cools down, the casting is carefully removed from the mold with extraction equipment.
As the centrifugal force compacts the aluminum, this method offers benefits such as improved material density, consistent wall thickness, minimal porosity, and enhanced mechanical properties. Still, this method is only limited to certain shapes, such as pipes, tubes, and other symmetrical, hollow components.
Open Mold Casting
Open mold casting is a basic technique that pours molten aluminum into a simple, open cavity. These molds can be made from brick, stone, steel, or sand. Unlike enclosed mold processes, the molten metal is exposed to air during cooling and solidification. This method is often used to create simple shapes like ingots or billets intended for subsequent processing like forging or machining.
The primary advantage of open mold casting is its simplicity and low cost, as it requires minimal tooling and setup. However, the resulting castings have poor dimensional accuracy, rough surface finishes, and may contain impurities due to air exposure. Also, open mold casting is generally unsuitable for producing finished parts requiring precise dimensions or intricate details.
Which Aluminum Casting Process Should You Choose?
The choice of aluminum casting process depends on your specific requirements. On top of costs, factors that must be carefully considered include the turnaround time, design accuracy, production volume, desired strength, required surface finish, and prototyping needs.
The following table provides a comparison of the primary aluminum casting processes discussed:
Casting Process | Permanent Mold | Die Casting | Sand Casting | Investment Casting | Centrifugal Casting | Open Mold Casting |
Turnaround Time | Moderate | Shortest | Moderate | Long | Moderate | Short |
Design Accuracy | Moderate | High | Moderate | Very High | Moderate (Limited to hollow, cylindrical shapes) | Low (Limited to simple shapes like ingots) |
Strength | High | High | High | Very High | Very High | Low |
Surface Finish | Good | Excellent | Poor | Excellent | Good | Poor |
Suggested Production Volume | Low to Medium | High | Low to Medium | Low to Medium | Medium to High | Very Low |
Prototyping | Less suitable | Less suitable | Most suitable | Less suitable | Less suitable | Suitable |
Even though it may seem difficult to choose the right process, partnering with an experienced manufacturer like Noporvis can provide expert guidance and ensure the best product outcomes. Feel free to contact us today to discuss your project requirements.
What Alloys are Used in Aluminum Casting?
Aluminum isn’t typically used in its pure form for casting. Instead, it’s alloyed with other elements like silicon, copper, and magnesium to enhance its properties for specific applications.
Different alloys offer varying characteristics, impacting factors like strength, corrosion resistance, and machinability. Choosing the right alloy is crucial for achieving the desired performance and functionality of the final product. For a quick comparison, the following table summarizes the compositions and properties of some common aluminum casting alloys which are listed with their American National Standards Institute (ANSI) codes:
Alloy | A360 | A380 | A383 | A413 | Alloy 43 | Alloy B390 | Alloy 218 |
Main Alloying Element | Si (9-10%), Mg (0.5-0.6%) | Si (7.5-9.5%), Cu (3-4%) | Si (9-11%), Cu (2-3%) | Si (12%) | Si (5%) | Si (16-18%), Cu(4-5%), Mg (0.45-0.65%) | Mg (7.5-8.5%) |
Tensile Strength (Mpa) | 170 | 320 | 310 | 290 | 230 | 320 | 310 |
Yield Strength(Mpa) | 170 | 160 | 150 | 130 | 100 | 250 | 190 |
Hardness (BHN) | 75 | 80 | 75 | 80 | 65 | 120 | 80 |
Elongation (%) | 3.5 | 3.5 | 3.5 | 3.5 | 9.0 | <1.0 | 5.0 |
Density (lb/in³) | 0.095 | 0.098 | 0.099 | 0.096 | 0.097 | 0.098 | 0.093 |
Melting Range (°F) | 1035-1105 | 1000-1100 | 960-1080 | 1065-1080 | 1065-1170 | 950-1200 | 995-1150 |
Die-Filling Capacity | Good | Moderate | Poor | Poor | Excellent | Poor | Excellent |
Machinability | Good | Good | Moderate | Excellent | Excellent | Excellent | Poor |
Corrosion Resistance | Moderate | Excellent | Good | Moderate | Moderate | Good | Poor |
Note that this table only provides a general overview. The specific properties of each alloy can vary depending on the casting process and heat treatment applied. If you are unsure about which aluminum alloy to choose, reach out to Noporvis today for expert advice based on your project’s unique requirements.
Are Aluminum Casting Products Recyclable?
Yes, aluminum is highly recyclable, making it a sustainable material choice. The aluminum recycling process is relatively straightforward: collected aluminum scrap is sorted, cleaned, and then melted down.
During the melting process, any coatings, inks, and other impurities are removed. Alloying elements can also be added at this stage to produce specific alloy compositions. The resulting molten aluminum is then cast into ingots, ready to be used again for casting or other manufacturing processes. This efficient recycling loop allows aluminum to be returned to the market as new products in a shorter timeframe.
Responsible manufacturers take environmental sustainability in aluminum casting to another level through their ESG efforts. For instance, Noporvis not only actively uses recycled materials where possible, but also optimizes manufacturing processes for energy efficiency while ensuring proper waste and wastewater treatment. This allows manufacturers to minimize their environmental impact and contribute to sustainable production practices.
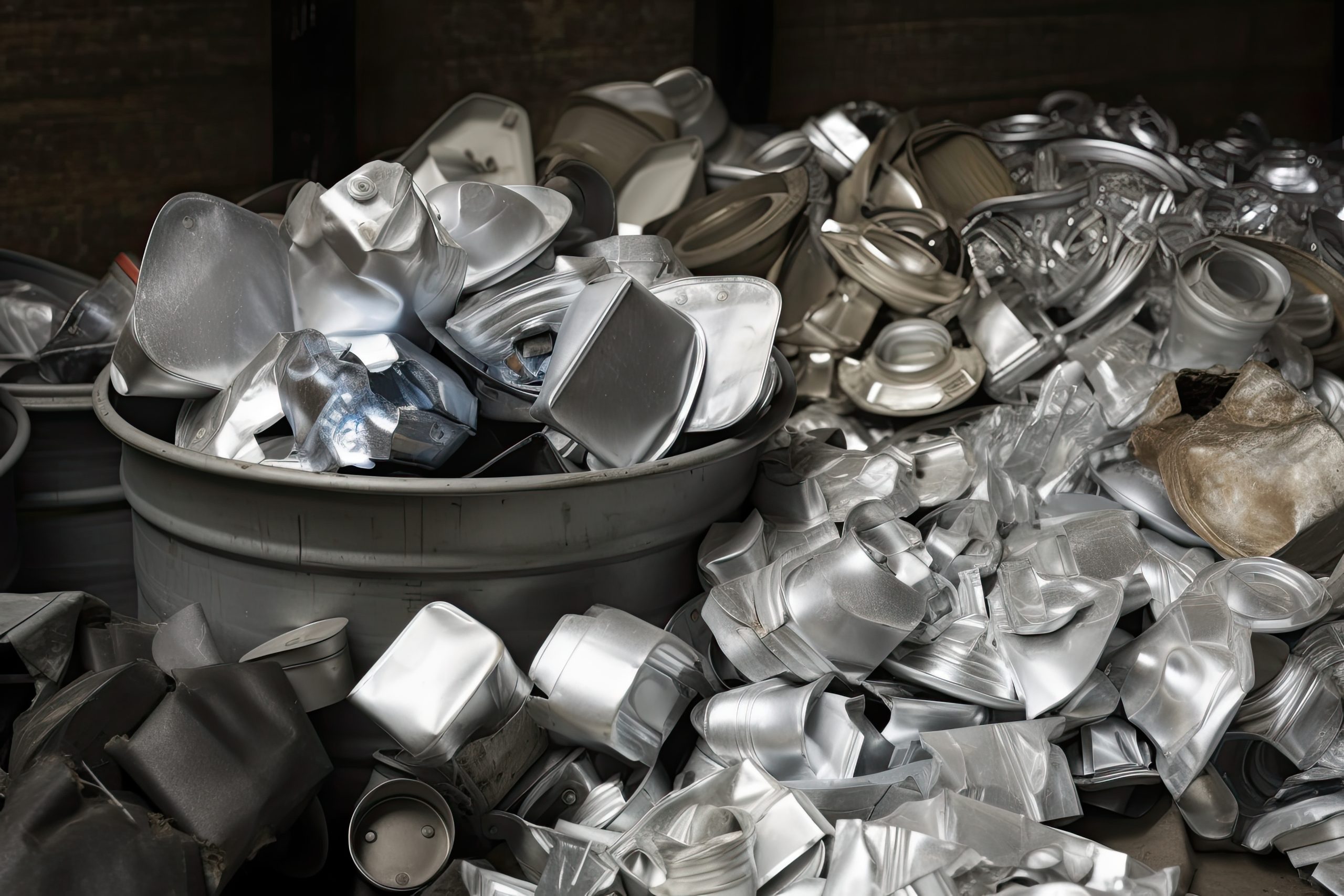
What are the Common Applications of Aluminum Casting?
Aluminum casting’s versatility makes it a critical manufacturing process across numerous industries, including:
- Automotive: Manufacturers rely on aluminum casting for weight reduction in vehicles, especially when producing components like engine blocks, cylinder heads, wheels, and turbine housing. This enhances the vehicles’ performance and fuel efficiency.
- Aerospace: With their exceptional strength-to-weight ratio, aluminum castings are preferred for aircraft components such as fuselages, wings, body structures, and engine parts, making up 60-80% of the weight in most commercial aircraft.
- Culinary: Aluminum castings are widely used in cookware due to their excellent thermal conductivity. As such, users can experience even heat distribution and efficient cooking with aluminum pots, pans, and grills.
- Lighting: Fixtures and housings for lighting are usually made with aluminum castings to ensure lightweight properties, corrosion resistance, and optimal heat dissipation. The aluminum casting’s fine surface also offers great aesthetics.
- Home Appliances: Refrigerators, washing machines, and smaller kitchen gadgets incorporate cast aluminum components for efficient operation and ease of handling which is made possible by aluminum’s lightweight and thermal properties.
- Medical: Surgical instruments, medical devices, and prosthetic limbs benefit from aluminum’s lightweight and corrosion-resistant nature, as well as precise manufacturing capabilities, allowing for safe and biocompatible equipment.
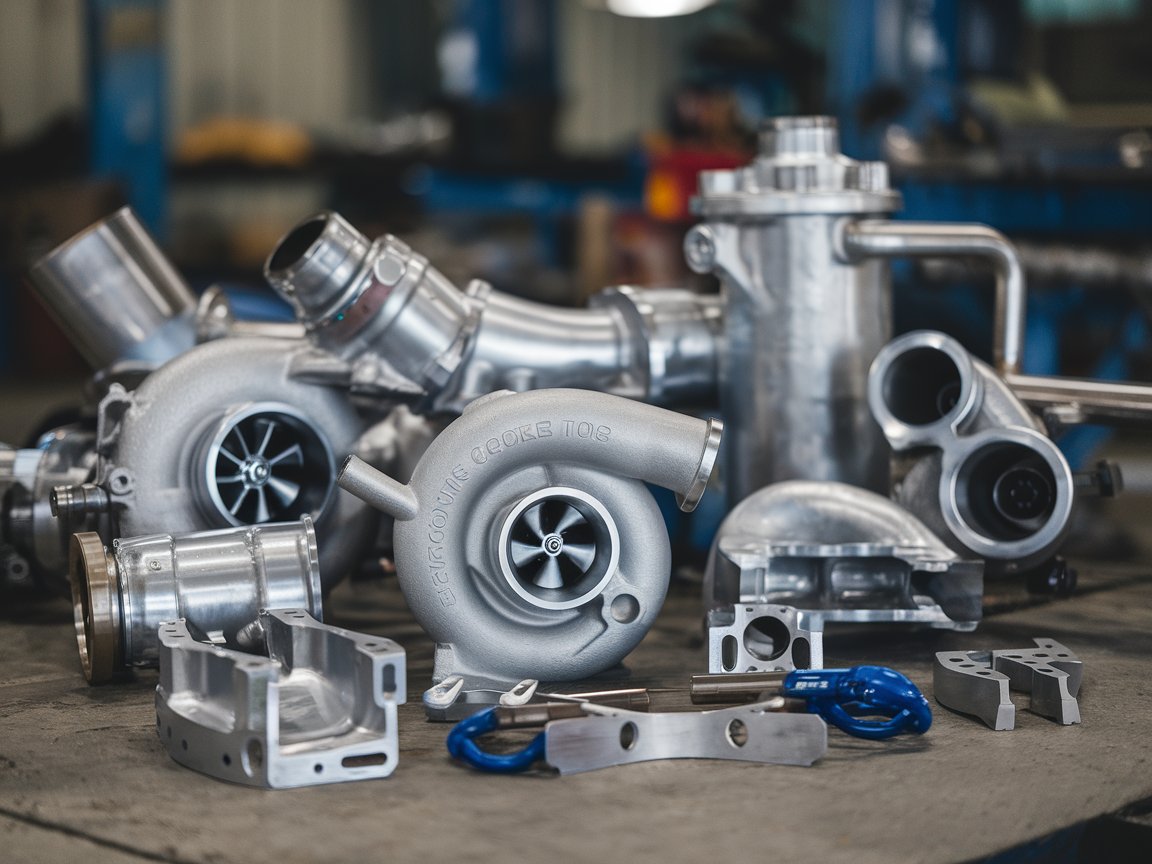
High-Quality Aluminum Casting Services at Noporvis
Noporvis stands out as a leading manufacturer aluminum casting manufacturer, offering high-quality products across diverse industries. Our specialty includes a wide range of OEM and aftermarket automotive components, from turbine housings to other critical parts.
Moreover, our commitment to quality is underscored by our ISO9001 certification and state-of-the-art facilities, ensuring exceptional precision and consistency in every casting. Noporvis also offers expert consultation to help clients select the optimal aluminum casting process and alloy materials for their specific needs, guaranteeing peak performance and durability.
Contact us today to discuss your aluminum casting requirements and discover how Noporvis can provide the ideal solution.
Frequently Asked Questions About Aluminum Casting
Q1. Is aluminum casting better than iron casting?
Not necessarily, both aluminum and iron castings have their own strengths and are suitable for different applications.
Aluminum casting is significantly lighter, offering a superior strength-to-weight ratio and machinability, making it ideal for conductive, weight-sensitive applications and components that require tighter tolerances. It also boasts better corrosion resistance and thermal conductivity.
Conversely, iron castings generally offer lower costs, higher strength, and great wear resistance. Due to this reason, iron casting is preferred for heavy-duty uses.
For more details about iron casting, refer to our article here: What is Iron Casting: Processes, Materials & Applications
Q2. What is the difference between cast and forged aluminum?
Cast and forged aluminum differ significantly in their manufacturing processes and resulting properties. Unlike casting which involves pouring molten aluminum into a mold, forging relies on compressive forces to shape a solid piece of aluminum.
Forged aluminum generally exhibits higher strength and fatigue resistance due to its refined grain structure. However, casting offers greater design flexibility, allowing for the creation of more complex shapes and intricate details that are often impossible or prohibitively expensive to achieve through forging. This makes casting the preferred method when design accuracy and complex geometries are crucial.
Q3. Are there any finishing processes for aluminum casting?
Yes, various finishing processes can enhance both the aesthetics and functionality of aluminum castings. Some common finishing processes include:
- Powder Coating: A dry finishing process where powdered plastic is electrostatically applied and then cured with heat, creating a durable and even coating.
- Painting: Applying liquid paint to the casting’s surface for color, aesthetics, and some level of corrosion protection.
- Electroplating: Depositing a thin layer of another metal onto the aluminum surface through an electrochemical process to improve corrosion resistance, wear resistance, or appearance.
- Anodizing: An electrochemical process that thickens the natural oxide layer on the aluminum surface, significantly enhancing corrosion resistance and surface hardness.
Q4. How to clean and maintain cast aluminum?
For routine cleaning, mild soap and water are usually sufficient. More stubborn stains may require a non-etching cleaner or turpentine. For a deeper clean, wax-based polishes or mild abrasives can be used, but harsh abrasives should be avoided as they can scratch the surface.
Regardless of the cleaning method, thoroughly drying the aluminum afterward is crucial to prevent water spots and streaking, especially around edges and joints where water can accumulate.